Aircraft Corrosion Sensing and In-Service Environmental Monitoring
Jeff Demo Electrical Systems Team Lead Intelligent Systems Group Exposure to harsh, corrosive environments during operational and on-ground activities can have significant contributions to aging and structural deterioration of aircraft. Reduction in aircraft system reliability presents a major cost driver in the total lifecycle costs as well as a threat to the safety. Environmental parameters, including temperature and relative humidity, as well as outside contamination sources, each play a major role in long- and short-term aging effects of aerospace structures and subsystems. To provide in situ measurements of environmental severity, Luna has developed and deployed the LS2A corrosion monitoring sensor suite (Figure 1). This system uses a wired or wireless sensor node to measure, record, and analyze environmental and corrosivity parameters including relative humidity, temperature, aluminum corrosion rate, and solution conductivity.
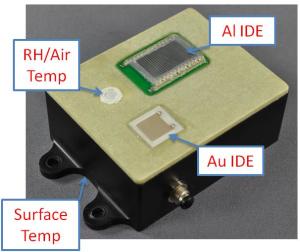
The January 2015 edition of Materials Performance magazine provided a feature article on the impacts of aircraft corrosion and how Luna’s LS2A system can be used to combat the rising costs of corrosion driven inspection and maintenance. After reviewing a 2014 NACE Corrosion paper written on the LS2A sensing platform, Materials Performance reached out to Luna to learn more about the technology and how it could best be used by aircraft operators and maintainers. One of the biggest challenges encountered when conducting an airframe inspection is reaching blocked, sealed, or obstructed areas. Inspections require maintainers to break seals, open panels, remove floorboards, etc. As a result, the simple process of performing the inspections can lead to additional contaminant ingress, and ultimately lead to more corrosion damage. Inspection and maintenance activities, as well as aircraft safety and operational availability, could be significantly enhanced for both fixed and rotary wing aircraft exposed to corrosive environments by using a corrosion monitoring system that identifies environmental conditions that lead to corrosion and also detects corrosion damage. As part of a Small Business Innovation Research (SBIR) program for the Naval Air Systems Command (NAVAIR), Luna developed a self-contained multi-modal corrosion sensor system, the LS2A, to measure, record, and analyze environmental and corrosivity parameters that affect corrosion susceptibility and corrosion rate of a material. The sensor technologies used in the LS2A system are integrated with an embedded low-power, wireless electronics package that collects and processes measurements from the sensors and reports both raw sensor measurement data and an ISO 9223-based environmental severity classification (C1 to C5) based on the sensor output. All sensor measurement histories, along with ISO environmental severity classifications are stored to the device’s internal memory and are available for maintainer download over wired or wireless interfaces. Since military aircraft typically have a long history of manual inspections, their maintainers generally have identified areas on each airframe that are known corrosion “hotspots,” such as underneath a helicopter’s floorboards or on its tail boom. A sensor node placed within these hotspot areas can provide the structure’s corrosivity information and corrosion rates to maintainers, enabling them to schedule manual inspections and maintenance actions based on the predicted condition of the structures. If data collected from the sensor nodes indicates a high level of environmental severity, this may drive an immediate maintenance action to inspect and repair corrosion damage. In the case of low severity classification, no actions may be required, and inspections may be skipped or delayed. The article goes on to discuss a five month deployment of the LS2A sensor nodes on a NAVAIR operated UH-1N rotorcraft, one of many deployment scenarios for the LS2A platforms to date. Deployment of the systems on an in-service UH-1N rotorcraft allowed Luna to collect and analyze real-world data and determine how the external conditions surrounding an airframe translate into the actual environmental exposure that is seen inside an enclosed aircraft. Through comparisons between data collected on the airframe and local National Oceanic and Atmospheric Administration (NOAA) weather station data, Luna was able to show that on-aircraft measurements can significantly improve a maintainers understanding of airframe exposure over simply relying on monitoring external conditions around the aircraft. Knowing how environmental parameters affect the corrosion susceptibility and corrosion rate of aluminum will help aircraft maintainers to schedule maintenance more efficiently, which can improve overall fleet safety, increase aircraft availability, and reduce operational costs. We invite you to read the full article put together by Materials Performance magazine and contact us with any comments or questions. We hope to be able to help you in your battle against corrosion, whatever your application may be.
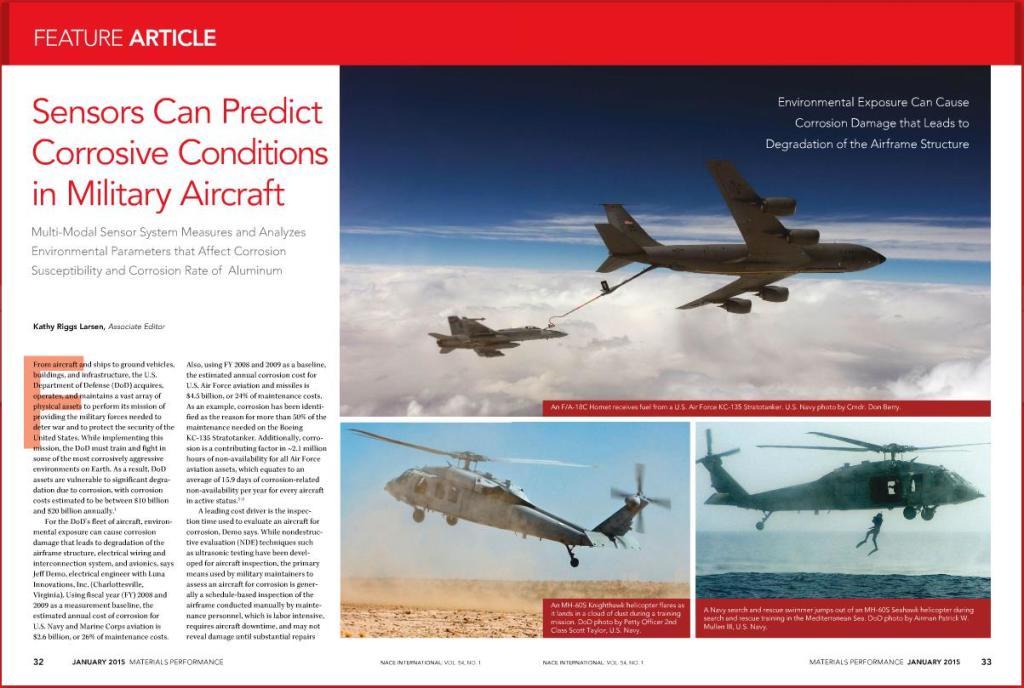