Enhancing Weapons Readiness: Fatigue Cracking Analysis for Gun Barrels
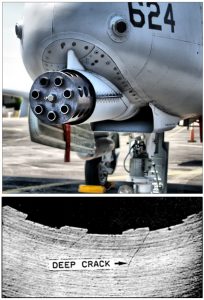
Every time a gun is fired, enormous gas pressures are generated inside the barrel to propel a projectile toward its intended target. For perspective, typical pressures can exceed 50,000 pounds of force per square inch: over three times the water pressure at the deepest ocean depths. The resulting stresses in the barrel’s wall impart fatigue damage each time a round is fired, initiating cracks that propagate radially through the barrel wall (Figure 1). The guns on military weapon systems feature a very high rate of fire. For example, the A-10 “Warthog” has a medium-caliber (30 mm) gun that fires up to ten rounds per second out of each of its seven barrels (Figure 1, top). At these speeds, fatigue damage can accumulate quickly.
Currently, maintainers do not have the inspection tools to quantify actual barrel fatigue damage in service. This is why the Air Force Life Cycle Management Center (AFLCMC) has sponsored Luna to invent technologies that will allow maintainers, for the first time, to quantify in-wall barrel fatigue damage as part of their current routine inspections. With improved knowledge of actual damage state, barrels may be retired based on actual condition instead of a highly conservative round-count.
Luna’s in-wall damage inspection system locates cracks using an electromagnetic probe that is scanned inside the full length of the barrel. The probe applies a time-varying (AC) magnetic field to induce small electrical “Eddy” currents in the barrel wall that flow in a closed loop around the barrel’s circumference and around the probe (Figure 2). In regions with no cracks, the currents flow near the barrel bore along the shortest possible path. As the probe scans through cracked regions, the current path is disturbed, requiring a detour around the non-conductive cracks. The resulting change in path length increases the electrical resistance along the path, thereby weakening the Eddy current flow. The probe’s sensing coil output is designed to increase in response to the reduced Eddy current flow, producing a rapid, non-destructive assessment of cracking damage in barrel walls. Critically, this electromagnetic technique is relatively insensitive to the barrel’s rifling grooves. Other NDE methods, particularly ultrasonics, are confused by the complex bore geometry and are not able to reliably identify nearby cracks. Luna’s technique has proven impervious to complex bore geometries and has successfully resolved the depth of cracks in 30mm caliber gun barrels. In this evaluation, Luna’s sensor output correlated very closely with the actual crack depth on a retired gun barrel. Luna is currently developing probes and techniques for 20 and 25mm barrels.
About gun barrel fatigue damage analysis:
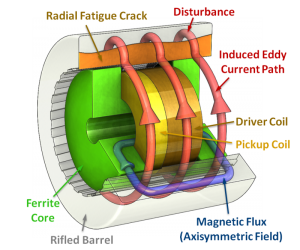
Damage progression rate can vary widely depending on the type of ammunition fired and the fatigue resistance of the particular barrel material. To avoid catastrophic barrel rupture and secondary damage to the weapons system, the barrels are retired after a specified round count experimentally determined ahead of time to be safe under the most conservative assumptions. Only after the barrel is removed from service, destructively cross sectioned, and visually inspected is the full extent of its fatigue damage known (Figure 1, bottom). In most cases, the cracks found in retired barrels are well under the allowable length, meaning that they were retired while they still had a significant amount of life remaining. Swapping barrels before they are fully expended effectively reduces weapons system availability and drives up operating and maintenance costs. Because of the high degree of uncertainty in barrel damage prior to cutting them open, this conservative approach is justified for avoiding the risk of a single catastrophic failure, loss of aircraft, and potential loss of life.
Today, maintainers commonly use surface profile inspection tools, such as laser-based scanners, that measure the condition of the barrel bore and rifling grooves that guide and stabilize the projectile. Bore and rifling condition affects the weapon accuracy, but is not the critical safety concern posed by through-wall cracks that are invisible to currently-fielded inspection methods. Luna’s in-wall damage inspection tool will locate cracks inside the full length of the barrel, resulting in enhanced aircraft and weapons system readiness.
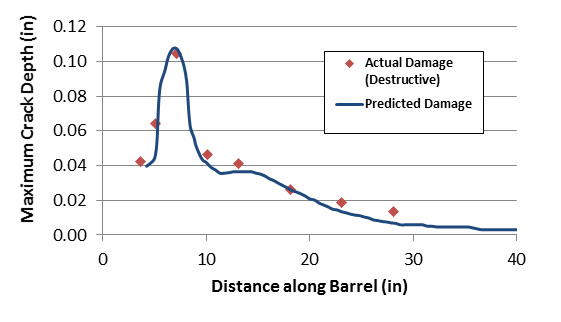