Luna Technology Used for Structural Health Monitoring at Cut River Bridge
The Cut River Bridge along U.S. Route 2 in Michigan’s Upper Peninsula was instrumented with Luna technology as a part of a research project to study the feasibility of a structural health monitoring system (SHMS) for monitoring the structural behavior, evaluating safety, mobility, asset management and planning applications using remote sensors.
The pilot project at the Cut River Bridge is a model that can be used at other bridge locations throughout Michigan, and lessons learned from this project will help MDOT with future implementations of SHMS at other bridge sites.
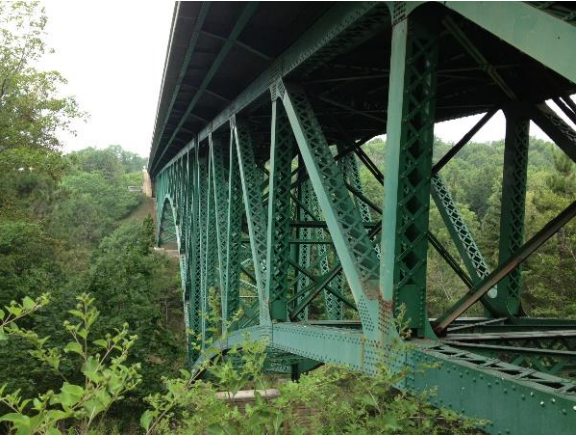
With the SHMS, the stress in the critical bridge members can be monitored and comparisons between the demand and the capacity of the structural member can be made. The monitoring serves as an early warning system for any potential overstressing in any structural member. This is especially important with a fracture critical structure where little to no visual warning may be given before a failure. When a threshold strain value for safety is surpassed, the system can be designed to alert MDOT and staff respond to a potential concern at the bridge. The SHMS can aid in determining load distribution between structural members, which may be an indication of section loss and changes in stiffness of the structure. With the accurate measurements of forces in the structural members, the ability of the structure to continue safely carrying traffic can be better estimated. This will help MDOT in planning any future repairs and assessing any risks associated with the bridge. The effectiveness of repairs can be monitored by comparing the strain values before and after a retrofit is made, which will also aid in estimating remaining service life.
The bridge was selected for the project due to its stand-alone, remote location without easy access to power, extreme weather conditions at the bridge site, and long distance communication challenges between the bridge and the staffed monitoring location.
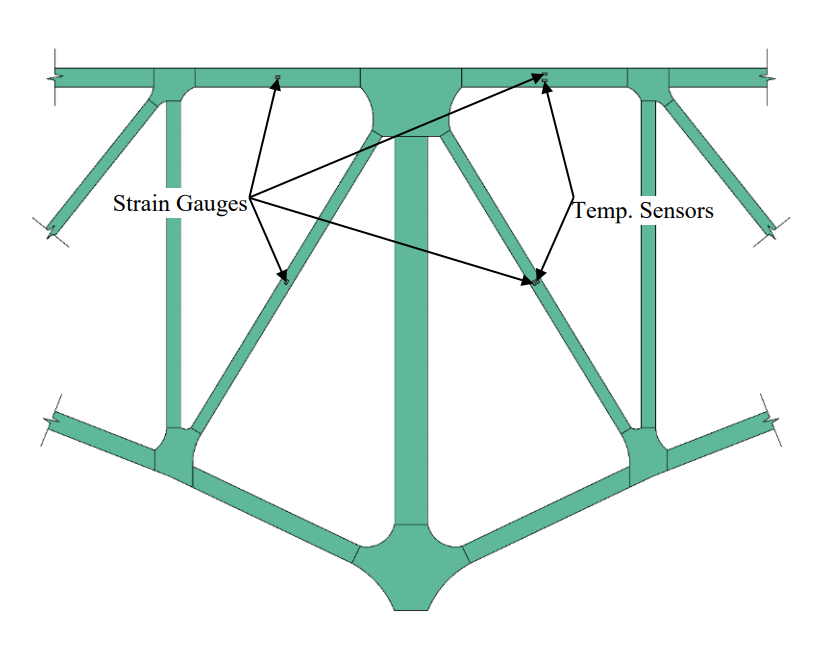
The Cut River Bridge is a three span, cantilevered deck truss bridge (one of only two cantilevered deck truss bridges in Michigan), 641 feet long and containing 888 tons of structural steel, and is considered a “fracture critical” structure, which means that there is a portion of the bridge that contains a steel component whose failure could cause a portion of the bridge to collapse. After the 2007 collapse of the I-35W Bridge over the Mississippi River, fracture critical structures have received additional scrutiny in an effort to prevent a similar catastrophic event from occurring. Typically, a fracture critical structure is inspected once every two years. However, the inspection will only observe and record defects visually or through non-destructive evaluation (NDE). The actual physical stress in the structural members of the bridge is not measured and can only be observed if a member is experiencing noticeable deformation.
To perform the structural health monitoring (SHM), 16 fiber optic Luna strain gauges (below) were installed on several primary tension members in the deck truss. In addition, four temperature sensors were mounted adjacent to four of the fiber optic strain gauges. The temperature sensors aid in correcting for any “drift” of the strain gauges due to temperature effects. In order to understand the truck loads that were crossing the bridge that were causing the observed strains, a weigh-in-motion (WIM) station was placed underneath the roadway approximately two miles east of the bridge. The WIM station provides axle weight and spacing for any truck traveling on the highway.
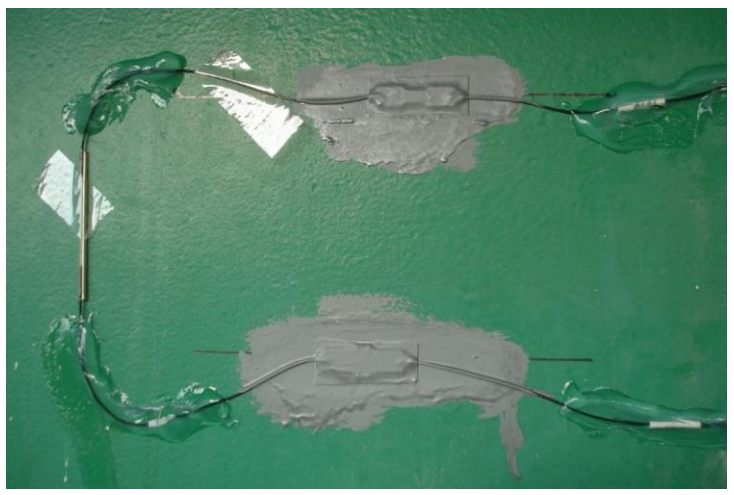
MDOT chose Luna’s fiber optic strain gauges for the many advantages they offered over traditional other strain gage types such as: greater strain range, longer fatigue life, not affected by surrounding electromagnetic waves, and faster sampling rates. The strain readings are corrected for thermal effect through temperature sensors. The strain gauge and the temperature sensors are designed to work together to provide accurate measurements of the strain in the bridge.
The strain gauges were installed at both the inside and outside faces at the north and south truss for a total of sixteen 16 locations. Temperature sensors were installed adjacent to the strain gauges only at one diagonal and one top horizontal truss member.
As light passes through the fiber optic cable and through the sensor, its wavelength changes as the strain in the Fiber Bragg Grating sensor changes and thus in the bridge member. The Luna (formerly Micron Optics) sm130 Optical Sensing Interrogator is connected to the sensors and used to continuously measure these wavelengths. It is powered by a 12V DC solar power system located in a concrete vault. The data from the interrogator is transmitted through the series of antennas and finally made available from any computer with an internet connection.
Data from the Cut River Bridge project was collected from a computer located at the bridge engineer’s office but could be collected from any computer with internet access. Another objective of the data collection process was to obtain weights and axle configurations of the trucks that cross the bridge as well as the strain in the bridge members caused by these vehicles. After the data was collected, it was processed to correlate the truck information with the strain information. This information is useful to make correlations between actual loads experienced by the bridge to the design loads according to current AASHTO and MDOT standards.
The strain information from the bridge was used to determine the live load strain caused by a moving truck, and were then compared to the maximum allowable strain to determine if the bridge members were overstressed.
The pilot project at the Cut River Bridge is a model that can be used at other bridge locations throughout Michigan. Lessons learned from this project will help MDOT with future implementations of SHM at other bridge sites.
For information on the Luna sm130, the HYPERION si255 interrogator or ENLIGHT software, contact us.
To read the full report by the Michigan Department of Transportation, visit this site.